Commutator FAQ
What is Compression Seasoning?
“Compression Seasoning” is the standard process for building a commutator. Many commutator manufacturers also refer to it as “Static Seasoning.” The standard process for building a commutator consists of a series of compressions and bakes at different times throughout the machining of the copper and mica pack. The formula for the number of bakes, bake times, and compression tonnage is determined by the commutator size, application, and speed that it will be operating at. For over 90 years Electric Materials has developed “static seasoning” processes that lead to unmatched quality and performance in our commutators.
What is Spin Seasoning?
Spin seasoning is the test done after the commutator has been Statically Seasoned or “Compression Seasoned”. During this test, Electric Materials will spin the commutator at or above the operating speed while applying heat. It is then cooled and the runout is recorded. This extra process ensures your commutator can withstand the operating speed and that you have a stable commutator. The spin speed is either supplied by the customer or our engineering team determines the speed based on the supplied operating speed and stress analysis. Majority of OEMs require their commutators to be spin seasoned.
Besides Spin Seasoning, does EM offer other testing or measurements to ensure the tightness of the Commutators?
Yes, Electric Materials offers profiling services. Profiling is done in line with the spin seasoning process. The profiling process will record any bar movement, at multiple locations along the brush surface, after the commutator has been spun. Measurements are taken before and after the spin cycle. In most cases, our customers set the parameters of our profiling process.
How do you manufacture commutator bars?
Electric Materials extrudes copper on one of our two extrusion presses and then we cold draw it to finish size. We have the ability to finish draw to a .0005” tolerance. During our cold drawing process, the commutator bar is cold worked to obtain the appropriate mechanical properties it requires to build a stable commutator. OEMs require commutator bars to be drawn to size to achieve these tight tolerances and mechanical properties.
What is Electric Materials Expertise with Commutators?
Electric Materials has been building commutators for OEMs for over 90 years. We have built for many OEMs such as: GE, WHSE, Reliance, etc. From working with many of these OEMs we have built a large database of OEM drawings that we can use to assist us in manufacturing new and old designs.
Can you Manufacture Mica V-rings without having a whole Commutator?
Yes, Electric Materials has a very large selection of Mica V-ring molds which we can use to make one-piece or sectional mica v-rings without copper or steel components. Our molds range from just under 2” to 121” in gage diameter.
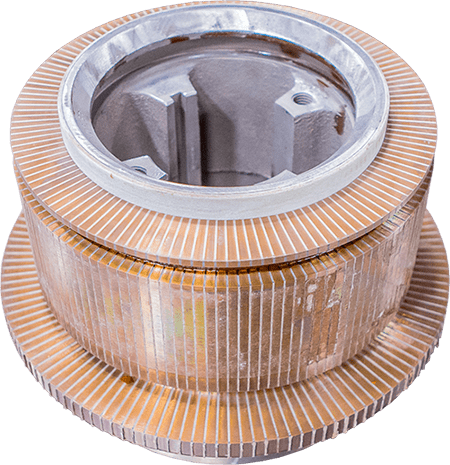